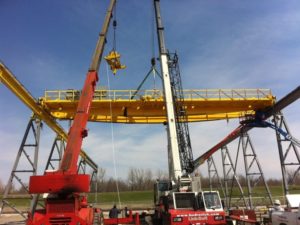
The Problems of Rail Misalignment
When crane rails and runways are not properly aligned, problems are going to develop. Both horizontal and vertical alignment are extremely important. When horizontal misalignment occurs, the crane’s wheels will experience excessive wear as the horizontal forces act against them (scraping/rubbing vs. gliding). Vertical misalignment causes the crane’s load to be unevenly distributed and results also in accelerated wear to multiple elements in the crane structure. Further, not only are the crane wheels and rail affected when rails are misaligned: we commonly see wear structural element fatigue and failure, as well as bridge couplings and axle wear patterns. Through recurrent misaligned operations, the crane itself can become skewed or flanged and experience binding on the runway, or dislocation of the crane from the rail altogether. In terms of efficiency, skewing and other types of misalignment can cause the crane to use more power to overcome the inconsistencies in alignment, making the crane unnecessarily inefficient and leading to premature failure of other electrical and mechanical components.
Based on these facts, it is safe to assume that ignoring rail alignment issues can prove both costly and dangerous.
Causes of Rail Misalignment
Crane rail misalignment can have many different causes, starting with an incorrect installation. When the installation is not performed correctly, the crane may not be fully square, the structure may not be properly aligned or the rail may note be properly aligned or a combination of all. Immediate issues should begin to propagate, most often illustrating in wheel metal shavings on the top of the beam or on the floor near the runway. Overloading a crane past its rated capacity and sudden impact loads can also lead to issues with misalignment. Settlement in the columns and/or support structure are additional culprits. All of these cases point to the need for regular crane rail and runway inspections. In the event issues are uncovered, a rail survey is an in-depth evaluation of the issues in order to confirm root causes for ultimate remediation.
Signs of Rail Misalignment
There are certain signs you can look for if you suspect your rails may not be properly aligned. These include the following common symptoms:
- Loud scraping sounds when the crane is in motion
- More power required to move the crane through certain sections of the runway
- Wheels that float or climb over the rails and then crash back down
- Wheel flanges that are cracked or completely broken
- Excessive wear on the rails, wheels, or wheel bearings
If you notice any of these issues, it is important to remember that just addressing the symptom (e.g., replacing a broken wheel or worn-out wheel bearings) will not solve the problem but just result in more repairs. If the issue is alignment, a rail survey needs to be performed to confirm and address with the real problem.
How Rail Surveys are Performed
A rail survey is performed using manual or electronic surveying tools to obtain key measurements related to the position of various points along the crane structure.
Rail surveys can be performed using traditional surveying tools as well as more modern 3D laser or camera equipment. The traditional approach uses a theodolite and geometric leveling, with the theodolite more commonly replaced with a laser now. In such an approach, a laser is mounted at the end of a rail and projects a point on a target board attached to a vehicle that moves along the rail. The position on the target board can then be read at specific distances and heights.
A more modern approach to alignment surveys makes use of lasers and automated tools. For example, alignment of high-level tracks can be accomplished using a laser auto-tracking total station at ground level to measure the distance to a robotic survey target (a prism) on the rail. With modern rail survey tools, the alignment, span, and level can all be obtained using the same setup. The rail survey service that you use may also use analytical software to fully investigate the data so that you can get as much information as possible about the condition of your crane rails.
Importantly and often missed, surveys should be performed in a loaded and unloaded crane/runway condition. Often, issues will not propogate in an unloaded scenario.
What to Expect from a Professional Crane Rail Survey?
Rail surveys will typically include the following:
- A visual inspection that includes observation of excessive wear as well as the assessment of rail gaps, rail joints, and rail clips
- Measurement of straightness, alignment, span, elevation, and rail-to-rail elevation
- Measurement of rates of change in structural elements between sections
- Data that shows where your rails are not within tolerances required by the Crane Manufacturers Association of America (CMAA)
- Full written rail inspection and survey report with recommendations
The crane rail inspection and survey report will include measurements, photographs, video footage, and calculations supporting the results presented in the report. In addition, you can expect to see the survey results compared to any standards that apply along with a full set of recommendations for how the crane rail and runway should be realigned for optimum performance. It is also common to see both 2D and 3D representations of the rails. In addition, the recommendations for addressing crane rail misalignment should propose ways to accomplish alignment by adjusting a minimum number of locations on the rail.
Conclusion
Proactively evaluating the health of your crane’s rail and runway condition will give you confidence in the reliability of your cranes. When properly performed, rail surveys can significantly reduce unplanned downtime and eliminate many costly repairs. In fact, with today’s technology, a service provider can quickly pinpoint potential issues before they happen (many times in real time with the proper equipment), further reducing unexpected downtime and many unnecessary repairs.
At Hi-Speed Industrial Service, you can count on our factory-trained technicians to use cutting-edge technology to perform a comprehensive rail survey for your cranes. In fact, we offer predictive maintenance service plans customized to your facility and its needs so that you can catch problems like rail misalignment before the damage is done.